Rapid prototyping creates a preliminary product version to evaluate the design and its functionality.
What is Rapid prototyping?
Rapid prototyping (RP) quickly creates a physical part directly from its CAD model data using various manufacturing techniques. Rapid prototyping can be used at any stage of the product development cycle for any components or sub-components. Prototyping can be repeated numerous times along the new product design process using the test data to achieve the desired part.
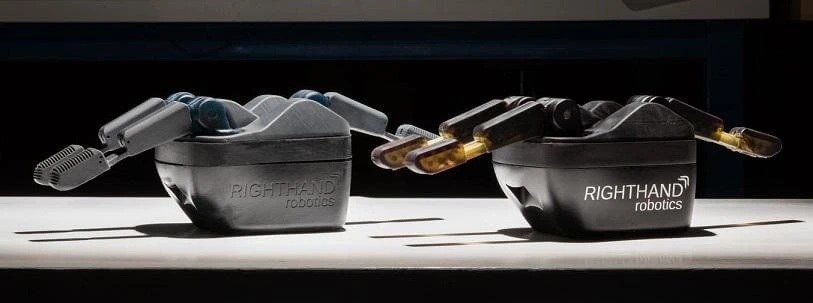
Rapid prototyping is a relatively new term and, in its simplest form, creating a prototype quickly to visually and functionally evaluate a part or some part features. Sometimes individual parts are rapidly created separately and assembled to test the prototype product.
So what is a Prototype? In an engineering product design context, a prototype is a preliminary version of the end-product used to evaluate the design, test the technology, analyse the working principle, and provide final product specifications. Prototypes are an integral part of engineering product design and, more importantly, in new product development.
Rapid prototyping & 3D Printing
Is rapid prototyping the same as 3D printing?
The simple answer is “No”. However, in the modern-day product development process, rapid prototyping is commonly used alongside terms like “3D printing” and “additive manufacturing”, mainly because 3D printing first came into prominence as a way of making prototypes quickly (Read more on the history of 3D printing).
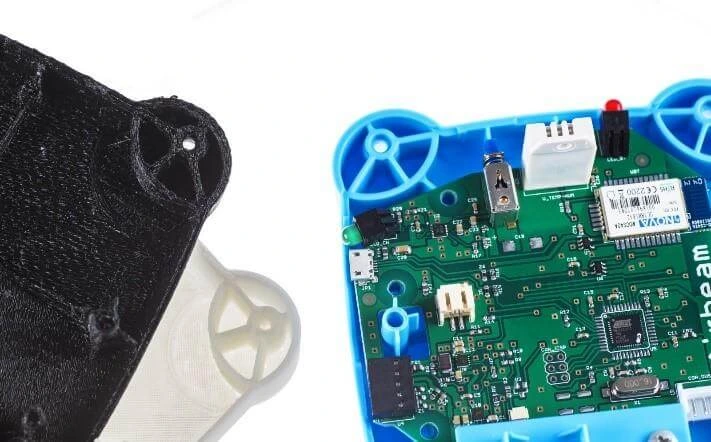
But the 7 types of additive manufacturing technologies have moved along and have made giant strides towards the production of quality parts and might not be the preferred choice for some prototypes due to higher costs.
So, what is the difference between rapid prototyping and 3D printing? 3D printing or additive manufacturing is a manufacturing process, while prototyping is the result or the end product. Furthermore, 3D printing on its own or other processes could be used to create rapid prototyping.
Why is Rapid prototyping important?
Companies need to develop and introduce new products faster to remain competitive in this fast-moving modern-day consumer market. Since faster product development and technology innovation are vital to a company’s success, rapid prototyping becomes the most crucial element of new product development. Rapid prototyping achieves the following objectives.
- Faster new product development – Rapid prototyping plays a vital role in the process of creating successful products because it speeds up the new product development process
- Early-stage design/concept validation of the form, fit, and function of the design
- Final stage product verification against the technical requirement and business objectives
- It allows functionality testing to test the objectives of the concept and to finalise the product specification
- The prototype gives the end-user, client, customer, user participants hands-on user experience to get feedback
Rapid prototyping applications
- Visual prototypes
- Concept models
- Functional prototypes
- Pre-production prototypes
- Production tools prototypes
- Production moulds for prototypes
Types of Rapid prototypes
It is crucial to understand the types of prototypes in product design before rapid prototyping your design. Generally, rapid prototyping is for individual parts rather than assemblies. Therefore, either more than one rapid prototyped part makes up an assembly, or a single rapid prototyped part is used to test and evaluate the complete form, such as a model.
Prototypes can be categorised depending on the degree of accuracy required, product development stage, and purpose.
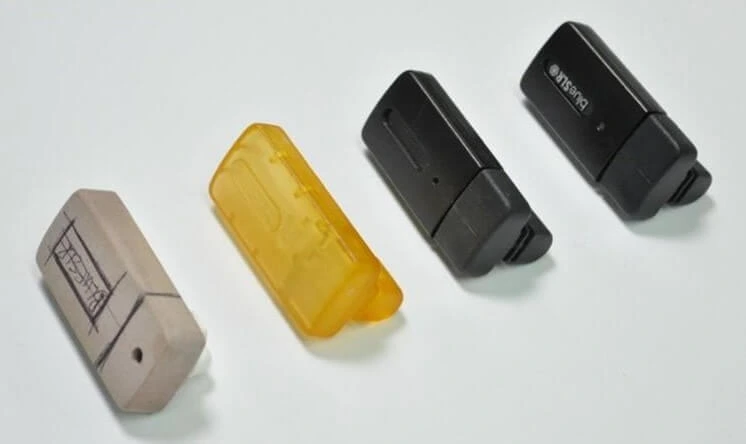
Rapid prototypes don’t necessarily need to look like final products and can vary depending on what the product designer is trying to achieve from the prototype. Rapid prototypes can be classified in terms of accuracy or “Fidelity”. The degree of prototype accuracy can vary from low-fidelity to high-fidelity in functionality, appearance, user interface, and size.
Low-fidelity prototype – Very simple and produced very quickly to test the broader concept. e.g. Paper sketches to cardboard mock-ups
High-fidelity prototype – These prototypes appear and function as similar and closer to the final product.
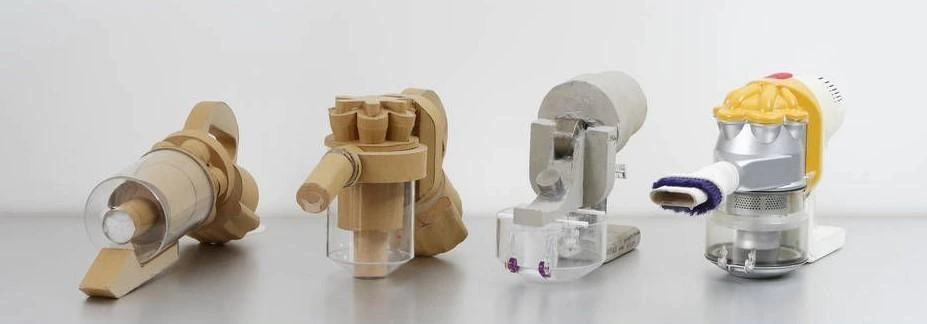
Advantages & Disadvantages of Rapid Prototyping
Rapid prototyping has pros and cons, like any manufacturing process.
Advantages of rapid prototyping
- Reduced design & development time
- Reduced overall product development cost
- Elimination or reduction of risk
- Allows functionality testing at a fraction of the cost
- Improved and increased user involvement during design stages of NPD
- Ability to evaluate human factors and ergonomics
Disadvantages of rapid prototyping
- Lack of accuracy – If the function of the product relies heavily on the accuracy of the parts, then rapid prototype parts and assembly might not be able to f the same accuracy
- Added initial costs – Rapid prototyping costs money due to technologies used and faster turnaround required.
- Some rapid prototyping processes are still expensive and not economical
- Reduced material properties like surface finish and strength
- Rapid prototyping required skilled labour
- Limited material range
- Overlooking some key features because they cannot be prototyped affects the prototype testing
- End-user confusion, customers mistaking it for the finished project/developer misunderstanding of user objectives
Rapid prototyping techniques
Choosing a suitable rapid prototyping technology is critical to the prototype’s success. Each rapid prototyping technique has its compromise in terms of cost, speed, material compatibility of the feature, fidelity level and development stage.
Stereolithography (SLA) | Binder Jetting |
Fused Deposition Modeling | Poly Jetting |
Selective Laser Sintering (SLS) | CNC Machining |
Multi Jet Fusion (MJF) | Vacuum Casting |
Direct Metal Laser Sintering (DMLS) | Investment Casting |
Rapid prototyping doesn’t need to be limited to one process; one can use more than one manufacturing technique to assemble a prototype.
Let us look at the Rapid prototyping techniques in detail:
Stereolithography (SLA)
Stereolithography (SLA) uses a laser to cure UV-curable resin to build parts from a pool of liquid resins. They are best for lower end functional prototypes, patterns, mould and production tools. SLA provides product designers and engineers with the ability to rapid prototype parts with excellent surface finish and good dimensional accuracy.
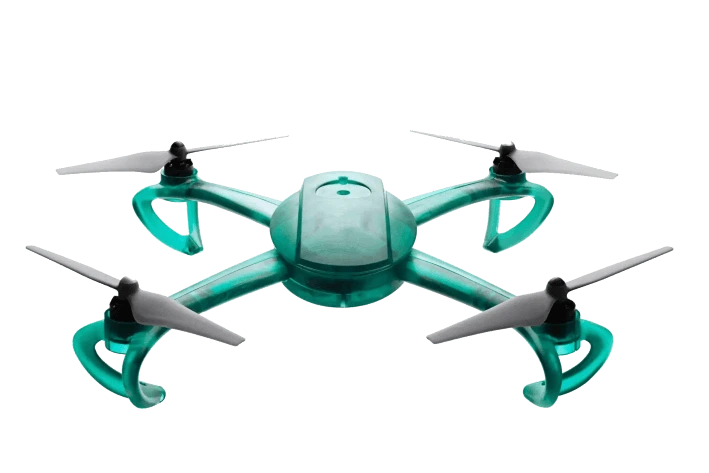
Learn more about understanding tolerance, accuracy, and precision in 3D printing.
Advantages | Disadvantages |
Reasonably priced | Low strength compared to other AM techniques limiting some functional testing |
Excellent surface finish for AM parts | Overtime resin becomes brittle |
Mature technology with a comprehensive material selection | Require support structures and slower speed |
Material – Tough and durable resins, flexible resins, elastic resins, rigid resins
Selective laser sintering (SLS)
SLS uses a laser to produce functional parts from polymer powder by sintering. Due to SLS parts’ internal porosity, they are brittle but have excellent tensile strength. Generally, SLS has a larger build volume and can generate parts with highly complex geometry and produce long-lasting prototypes.
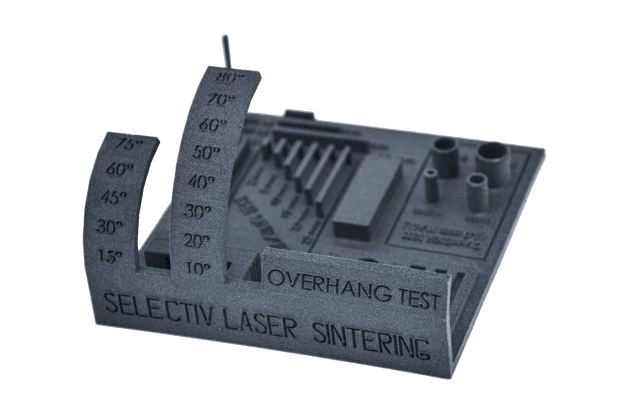
The technology’s low cost per component, high productivity, and proven materials suit various applications ranging from quick prototyping to small-batch manufacture.
Advantages | Disadvantages |
Durable with excellent accuracy | Rough surface finish with a grainy texture |
Support structure not required | Limited choice on resin material |
Suitable for dying and colouring | Porous and brittle structure |
Material options – PA11, PA12, PA12 40% glass filled, PA12 Carbon filled, TPU, PA12 – flex
Direct metal laser sintering(DMLS)
DMLS is an additive manufacturing technology that involves melting and fusing layers of metallic powder using a computer-controlled, high-power laser beam.
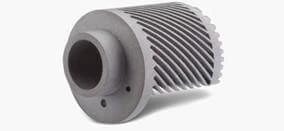
If designed to suit both applications, it can rapidly prototype Metal Injection Moulding (MIM). In addition, most alloys may be used in DMLS, allowing prototypes to be full-strength, functioning hardware produced of the same material as production components.
Advantages | Disadvantages |
Wide variety of metal alloys | One of the slowest |
Excellent material properties | Expensive |
Produces shapes and features that are difficult to make using conventional CNC machining | Specialised manufacturer |
Material – Aluminum alloys, Stainless steel, Titanium and some alloys
Fused Deposition Modelling (FDM)
FDM technology creates 3D parts by melting and extruding thermoplastic resins onto a Build platform layer by layer and letting it re-solidify.
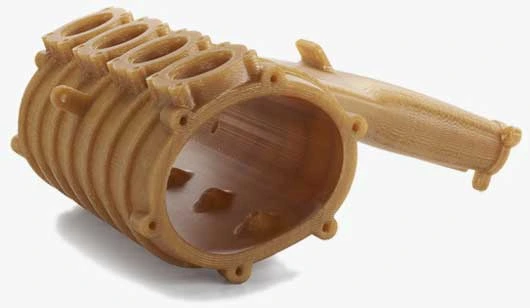
Because of their capacity to print in recognised polymers and composites, FDM printers have an edge in generating sturdy, useable, long-lasting parts.
Advantages | Disadvantages |
Comparably cheaper compared to SLA and SLS | Moderate surface finish – ripple effect due to layering |
Possible to make complex shape parts | Low strength in Z-axis due to layering |
Thermoplastic resin to prototype parts such as ABS, polycarbonate, or PC/ABS | Limited suitability for functional testing |
Material – ABS, PC-ABS, PC, ASA, Nylon
Multi Jet Fusion (MJF)
Multi-jet fusion is a powder bed fusion 3D printing technology in which fusing agent bonds powdered material and then heats to fuse them to produce 3D parts. MJF can print highly accurate and durable rigid parts using Nylon PA11, PA12 Nylon and PP. They can also print flexible TPU parts.
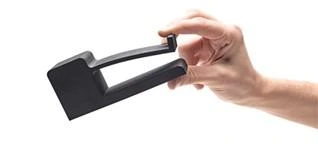
Advantages | Disadvantages |
One of the fastest 3d printing | Limited material choice |
No support structure due to powder bed | Surface finish is rougher than SLA and Polyjet |
Excellent surface finish and mechanical and physical properties | Expensive equipment costs might drive the part cost up |
Binder jetting
Binder jetting is one of 7 additive manufacturing technologies that can produce metal and colour plastic parts. Compared to DMLS, they are very cheap to make metal prototypes. In binder jetting, the binding agent is selectively deposited into a powder bed where it solidifies to create a 3d part.

They can be used to prototype full-size assemblies as a model to test user interaction
Advantages | Disadvantages |
Comparable cheaper | Rough surface finish |
Faster process | Not suitable to functional testing to low strength |
Both metal and plastics are available | Limited material choice |
Poly jetting
Polyjet is a material jetting technology that produces smooth and accurate parts. The technology uses photopolymer to create parts by jetting onto the build platform and curing them using a UV light.
The surface texture, colour, and different properties are crucial for concept models and full assembly prototypes to test user handling.
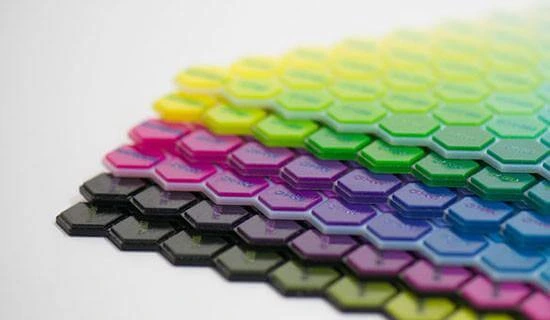
Advantages | Disadvantages |
Reasonable cost to print | Low strength |
It can print thin walls and complex geometries | Not suitable for functional parts or testing |
Both rigid and flex material can be built onto the same part | Not suitable for outdoor use or testing |
Material – General purpose resins – Rigid – opaque and transparent, Flex
CNC Machining
For parts where its functionality relies on high accuracy and tolerance, CNC machining is still the best prototyping method available. CNC machining is a subtractive manufacturing process in which blocks and rods of metal and engineering plastics are milled and turned to create highly accurate complex parts. There is a wide variety of materials available to cater for any application.
For rapid prototyping CNC parts, consider only the critical features that need machining and break down the parts, so only the critical part of the prototype are machined.
Advantages | Disadvantages |
Excellent accuracy and surface finish | Geometry limitations |
Wide material choice | Expensive due to setting up and tooling cost |
Higher-strength and suitable for all sorts of functional and environmental testing | Very limited in house capability due to equipment cost |
Vacuum casting – Urethane casting
Vacuum casting or Urethane casting uses silicone moulds to make plastic and rubber components under vacuum. They are one of the best processes to rapid prototype injection moulding plastic parts. Therefore, they are ideally suited for small to medium pre-production parts that can be used for functional testing.
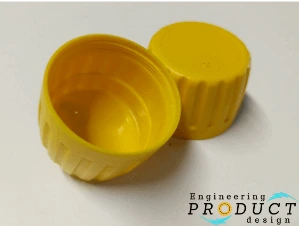
Advantages | Disadvantages |
A wide range of vacuum-casting resins are available | surface finish depends on the post-processing of the part |
Aluminium and brass in-mould inserts | Thin and thick features may deviate from standard tolerance due to shrinkage |
create small batches of high-quality injection moulding-type parts for prototype | wears out quickly and generally lasts for about 30 – 50 parts |
Material – Polyurethane resins to mimic rubber, ABS, Acetal, PP and even glass-filled nylon.
Investment casting
Investment casting creates parts using wax patterns coated with refractory material to make an expendable mould. Then the wax pattern is melted away before pouring molten metal. Once the metal solidifies within the mould, the foundry breaks the refractory mould to remove the cast parts.
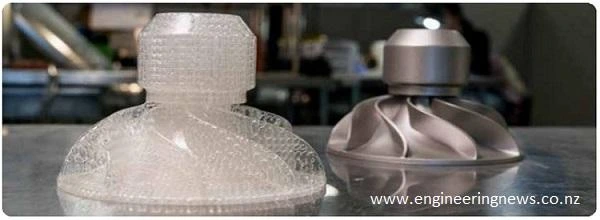
Investment casting is an excellent process to rapid prototype Die casting parts. Investment casting and 3D prototyping techniques such as FDM and SLA produce high precision master patterns with ultra-fine detail and a smooth surface finish.
Advantages | Disadvantages |
Possible to cast parts with highly complex shapes and intricate features | Available for metal parts only |
Excellent dimensional accuracy and tighter tolerances | Parts are difficult to cast if they require cores |
Excellent surface finish | Costly refractory material and labour cost |
Material options – Although a large selection of metal is available for investment cast prototypes, use Aluminium alloy unless the material is vital for functional testing.
Share this post on